Senior Lecturer
Engineering Discipline
Research Institutes
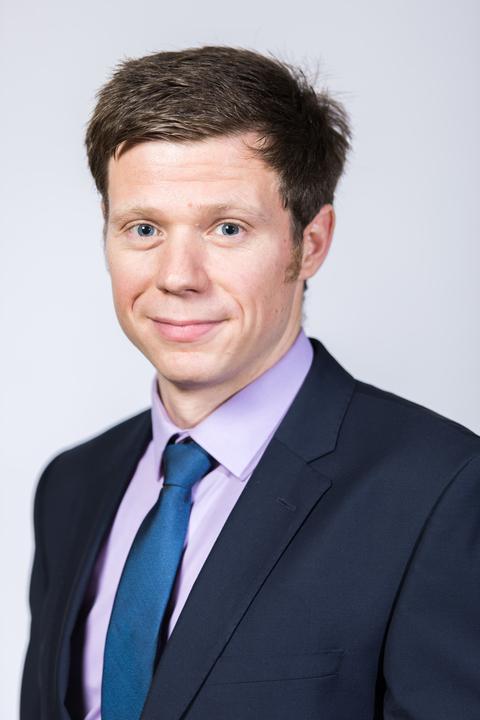
I am a Lecturer in Mechanical Engineering within the Institute for Energy Systems (IES) at the University of Edinburgh. My background is in energy storage, marine energy testing facility design, and turbomachinery.
My current main interest is energy storage, which will be a key component in the low carbon sustainable energy systems of the future. Energy storage is currently the missing link between energy use and the temporal variation in the power supplied by renewable generation. I am currently working to resolve some of the key challenges related to energy storage, recovery and engineering at ultra-high temperatures. Storage at such temperatures would unlock energy densities superior to mechanical and comparable to electro-chemical methods, whilst not being limited by location or cycle degradation, or the need to use rare construction materials.
My other interests include improving our ability to generate sea-representative conditions within experimental facilities. To this end I have pioneered the “isolating inlet” and the “water-wave filter”: the isolating inlet allows waves and currents to be combined at greater speeds than ever before whilst maintaining realistic turbulence levels; the water-wave filter is the first useful tuneable passive filter known in fluid dynamics and can be used to remove the high frequency reflected waves that cannot be absorbed by a force-feedback wave-maker, consequently improving test realism and accuracy. Both discoveries have allowed step changes in test tank capabilities and are enabling technologies for fully 3D combined current and wave test tanks like FloWave. My current research in this area is focused on combining wind, wave and current flows accurately within experimental test facilities.
My doctoral work involved “Computational investigations into offtake flows with application to gas turbine bearing chambers” and was undertaken with Rolls-Royce at their University technology centre at Nottingham University.
I have worked extensively in industrial environments and have extensive design and project management experience in the aerospace sector. Having created numerical design tools for Rolls-Royce and worked on the bearing chamber cooling and lubrication system development within the Trent 1000 and BR725 engine programs. Earlier in my career I was employed as a project manager within the Rolls-Royce supply chain. I began my profession in engineering as a technical apprentice in press tool design. I am proud to have been awarded Chartered Engineer status and elected a member of the ImechE in recognition of my work in industry and academia.
- 2010, (PhD), ‘Computational investigations into offtake flows with application to gas turbine bearing chambers’, University of Nottingham, funded by Rolls-Royce
- 2006, Meng with distinction, Aerospace Systems Engineering, University of the West of England, Bristol.
- Chartered Engineer and member of the Institute of Mechanical Engineers (ImechE).
- Conceptual design for mechanical engineers 3.
- Mechanical engineering design 3.
- Mechanical design principles 3.
- Engineering design 1
Postdoctoral research associates
Dr James Young
“Materials for ultra–high temperature in energy storage and energy recovery”
Thermal energy storage has been limited, until now, to temperatures around 800 K. If this storage temperature can be raised without incurring unacceptable thermal losses, energy density and conversion efficiency to electricity could reach a point where grid-scale thermal storage becomes technically and economically attractive. At ultra-high temperatures (1800 K) radiative losses dominate. Although these emissions can be reduced, there is a limit beyond which energy losses can only be recovered through a heat pump. For a heat pump to survive these challenging temperatures, new materials and approaches are required to produce the critical components such as compressors, turbines and heat exchangers. To achieve high efficiency, compressors and turbines have highly stressed blades operating at elevated temperatures. For heat exchangers to achieve maximum surface area and therefore energy transfer within a compact volume, they must have a thin-walled honeycomb structure. The most important failure modes that must be considered at ultra-high temperatures include creep, oxidation, thermal shock, and fracture. These have been investigated in this project along with microstructural changes, wear and erosion, vibration, fouling and fatigue.https://www.eng.ed.ac.uk/about/people/mr-james-young
PhD students
Thibaut Desguers
“Ultra-high temperature heat transfer analysis and thermal insulation design”
With the advent of ultra-high temperature technologies (e.g. thermal energy storage), novel insulation designs are needed to prevent energy losses which can occur through convection, conduction or radiation. While a vacuum is an efficient solution against the former two, the latter proves more challenging. Within this framework, my work focuses on the theoretical, numerical and experimental modelling and analysis of mixed ultra-high temperature heat transfers in non-grey, semi-transparent and evacuated composite structures with temperature-dependent thermal conductivities. Specific geometries are studied that would provide both efficient high-temperature thermal insulation and sufficient mechanical support to sustain their surrounding structures
Aldo Eyres
“Modelling and optimisation of gas-solid heat exchangers”.
A modified Brayton cycle is employed to extract energy from the UHTS system. This cycle has been modified such that its source of heat is the high temperature core instead of a typical combustion chamber. Gas-solid heat exchangers are used to transfer heat from the solid core to the working fluid in the cycle. In order to optimise these heat exchangers, I am producing a numerical design tool that will predict the heat transfer rates and working fluid pressure losses for a specified heat exchanger design.
Haris Hussain
"Feasibility study of integration of UHTS with electrical grids "
This project aims to develop a numerical time-domain energy system model for optimization of ultra-high temperature thermal energy storage operated within national electrical grids. The performance evaluation is based on various relevant elements such as heat and electricity demand profiles, share of renewable energies in the system, charging/discharging cycle behavior, UHTS plant sizing and layout, operational reliability and cost competitiveness. This will lead to a deeper understanding of all relevant parameters, variables and constraints which contribute to optimum operation and design of ultra-high temperature thermal storage system at grid level.
Tarek Abdelsalam
“Ultra-High Temperature Thermal Energy Storage for Concentrated Solar Power”
This project investigates the potential of integrating a novel Ultra-High Temperature (>1500 K) thermal energy Storage (UHTS) system with concentrated solar power (CSP) technologies. This involves tackling technical challenges that restrain current CSP technologies from operating at temperatures higher than 1000 K. This integration will not only improve the economic feasibility of UHTS through sharing infrastructure and storing heat directly at point of generation but should also enable CSP power cycles to operate at a much higher temperature, which can have substantial thermodynamic benefits (theoretically estimated to enhance the thermal efficiency of power generation by 50%).
Sebastian Hudson
“Integration of an Ultra-High Temperature Energy Storage System into Conventional thermal Power Generation Sites.”
Description: This project investigates implementation of an Ultra-High Temperature Thermal Energy Store (UHTS) at existing power generation sites. The store may be discharged through the heating of an air stream which may provide an alternate heat source to power a turbine, reducing the fuel requirement. The benefits are to be quantified by the effect on the flue gas composition, investigated with the use of Computation Fluid Dynamics and validated with experimental data. The required alterations to existing turbines to allow the system to successfully operate are also to be outlined and designed.
James Ferguson
As second supervisor:
William Jamieson “Materials & Manufacturing Optimisation for Curved Wave Energy Device”
Sam Thompson